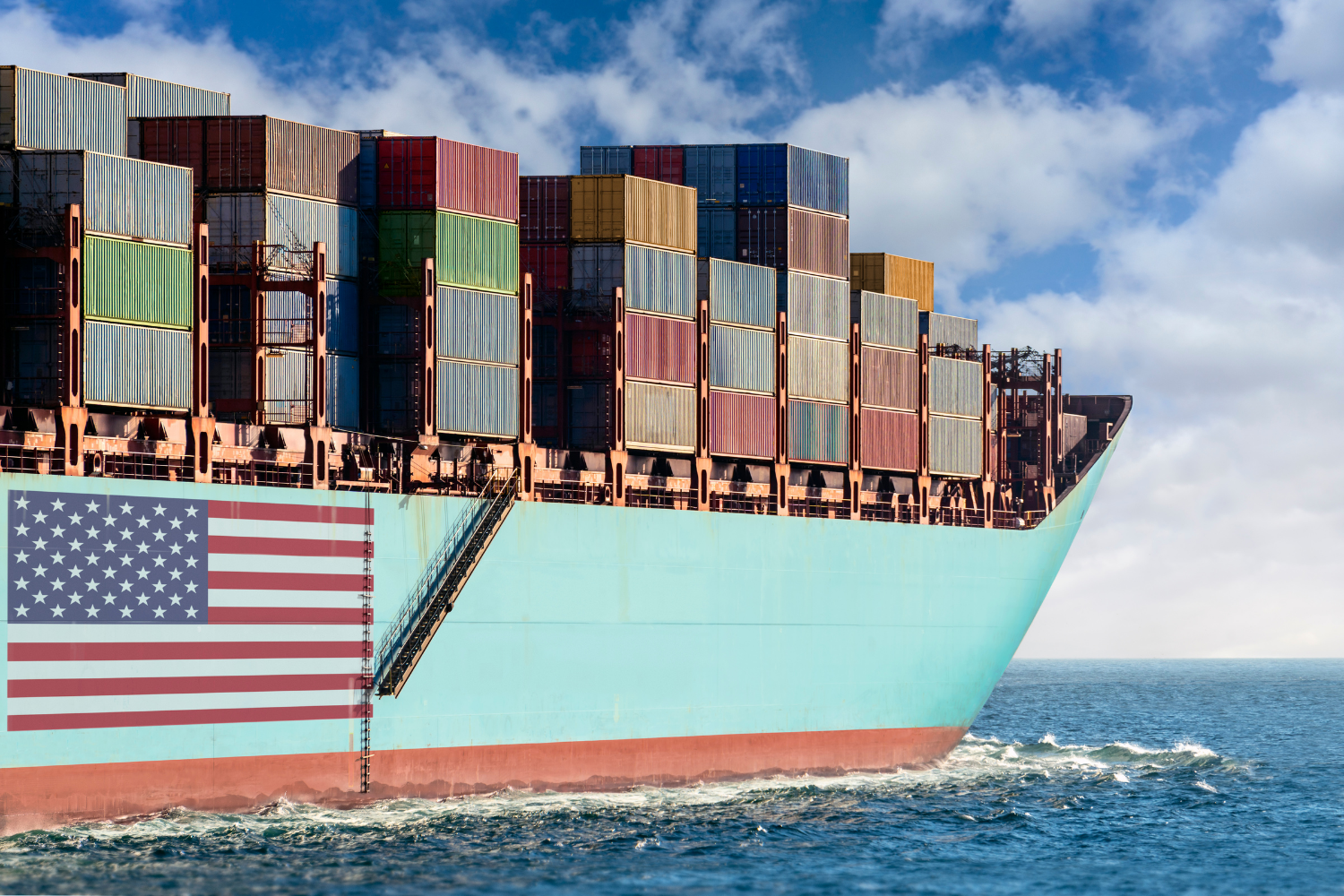
The Knot in Our Supply Chains
Written by Andrew Roth, Financial Advisor
My wife and I received our dining room table nearly 11-months after the original delivery date. Objectively, this seems like a peak “first-world problem,” but every time I looked at the stand-in card table, I wondered what is going on with supply chains?
People have long bemoaned the outsourcing of manufacturing. Since the 1970s, American manufacturers have increasingly shifted production overseas. This effort to maximize profit is now the norm, not just for U.S. businesses but for all developed nations. Outsourcing allows for low-cost consumer goods, maximizes profits, and (arguably) allows developed economies to focus on more profitable enterprises like high-tech pursuits and professional services. Despite its status as a political hot-potato, this trend was running smoothly until recently.
The 2020 pandemic threw a massive wrench in global supply chains that may take years to resolve. Pundits are even theorizing that much of the price inflation we are feeling is caused by a massively lopsided supply and demand imbalance. In the United States, demand for goods persisted during the pandemic. At the same time, foreign factories were shuttered due to lockdowns—some of which are still ongoing.
Virtually everything we consume is imported in-whole from overseas or dependent on foreign components and materials. The amount of product imported into the United States each year is astounding. In 2019 it is estimated that we imported $2.5 trillion worth of goods.
To put things in perspective, the number of container ships, some over one-thousand feet long, stands at about 5,200. Each ship can carry an average of 21,000 TEUs (Twenty Foot-Equivalent Units) using either standardized 20-ft. or 40-ft. steel containers. The largest of these ships can move cargo equivalent to a 40-mile-long freight train. Everything being imported around the global must move across the oceans in uniform steel containers, then be unloaded, sorted, and sent toward final destinations.
In May, the Port of Los Angeles reached a milestone by handling 1 million TEU’s (if my math is right, a half-million 40 ft. containers). They’ve stated that cargo volume is up 48% compared to the same period in 2020. This stands in contrast to last year’s backups, which caused ships to loiter for weeks before being unloaded due to dockworker restrictions. There is no sign things will slow as merchants struggle to satisfy demand and backorders, and port infrastructure strains under the volume.
This desperate demand for shipping capacity means that many cargo carriers are foregoing loading empty containers before heading back the other direction. This furthers the supply chain problem and leads to container shortages overseas. The Port of LA reported that the number of empty containers it was storing is up 114%.
Discouragingly, the problem cannot be solved by quickly building ships or conjuring new containers. According to ING, there are open orders for approximately 230 ships, with a combined capacity of 2.2 million additional TEUs, but these ships will take years to get into service. On the container side, three Chinese companies produce around 80% of the world’s containers. These companies are increasing output, but only projecting an additional 6%-8% increase in production.
Bottlenecks in shipping abound. This shortage is showing itself in both container and shipping prices as the price for a new container is now $3,500 per unit versus $1,800 in early 2020. Shipping rates quoted between Shanghai and Los Angeles were up 197% year-over-year. The surge in pricing is being felt everywhere.
These problems are unlikely to be resolved soon, causing unhappy consumers, spotty inventory, missed revenue, and increased costs. At some point, merchants may be required to start passing these costs along to customers as they become harder to manage and to predict. Just-in-time production and outsourced manufacturing works, up until the moment it doesn’t.
Many of us are experiencing this inconvenience for the first time in our lives. In a world where Amazon Prime can deliver to our door next-day, many people have forgotten how fragile the global logistics system can be.
While these are minor pains in the grand scheme of things, it could be enough to cause U.S. companies to evaluate how lean they run their supply chains, the amount of inventory they keep on-hand, and perhaps consider re-shoring their manufacturing. From a consumer standpoint, it’s possible this is the pain people need to put their money where their mouth is, and finally demand to “Buy American.” Maybe we will see a resurgence in agile and smaller-scale American manufacturers. Perhaps we can build a stronger and more robust system moving forward.
This content is developed from sources believed to be providing accurate information. The information in this material is not intended as tax or legal advice. It may not be used for the purpose of avoiding any federal tax penalties. Please consult legal or tax professionals for specific information regarding your individual situation. The opinions expressed and material provided are for general information, and should not be considered a solicitation for the purchase or sale of any security.